McAfee Speeds to Market with OEM Alliance Solution
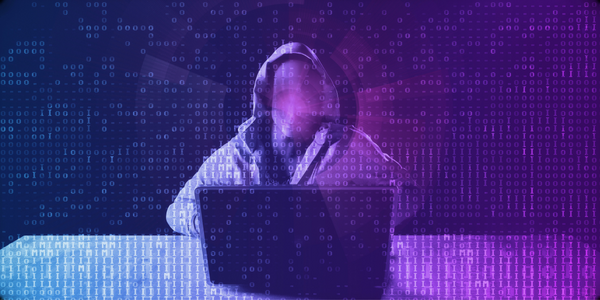
- Processors & Edge Intelligence - System on a Chip
- Product Research & Development
McAfee, the world’s largest dedicated security technology company, delivers proactive and proven solutions and services that help secure systems, networks, and mobile devices around the world. With over $600 million dollars of procurement per year, McAfee relies on its dynamic OEM appliance manufacturing partners to develop extremely reliable, high-performance new products quickly and efficiently. Most importantly, McAfee requires its suppliers to deliver the same high-quality engineering and support that its customers have come to expect. In any product lifecycle, flexibility is the key ingredient to a successful deployment. During McAfee’s development of a new turnkey solution, Intel announced the introduction of new processors, which would become generally available at the same time as the planned debut of the McAfee appliances. Being able to take advantage of these new processors without delaying the introduction of the new appliances introduced a new challenge and McAfee needed a partner to step up to remove the potential obstacle.
AMAX took the initiative to leverage its strong relationship with Intel, obtaining the new processors before they were released to the market and early enough in the appliance design process to streamline McAfee's product and system testing. The new appliance also featured specific drivers to maximize availability, gold-level redundant power supplies, and remove system management capabilities to meet McAfee's exact requirements.
Case Study missing?
Start adding your own!
Register with your work email and create a new case study profile for your business.