Continuous Emission Monitoring Systems
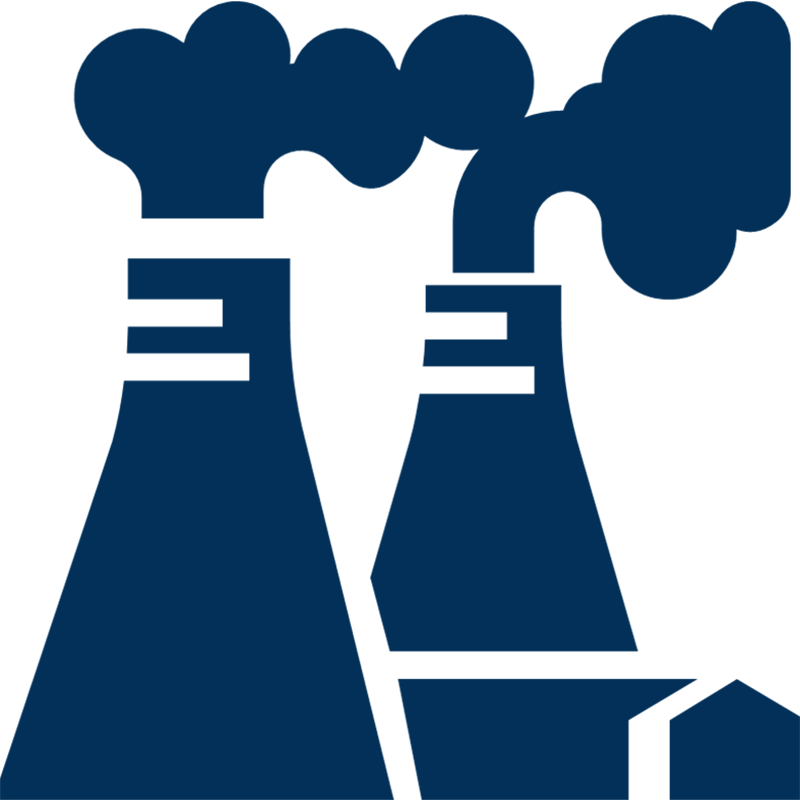
Continuous emission monitoring systems (CEMS) measure airflow, dust, the concentration of air pollutants (such as SO2, NOx, CO, etc.), and other parameters related to emissions. Required parameters depend on the type of stationary source and local regulations. A standard CEMS consists of a sample probe, filter, sample line (umbilical), gas conditioning system, calibration gas system, and a series of gas analyzers that reflect the parameters being monitored. Typically monitored emissions include: sulfur dioxide, nitrogen oxides, carbon monoxide, carbon dioxide, hydrogen chloride, airborne particulate matter, mercury, volatile organic compounds, and oxygen. CEMS can also measure airflow, flue gas opacity, and moisture.
- Energy
- Chemicals
- Discrete Manufacturing
The emission monitoring systems market is expected to reach USD 4.44 billion by 2025 from USD 2.39 billion in 2018, at a CAGR of 9.3% between 2018 and 2025.
Source: PR Newswire
The gas analyzer market is projected to reach USD 4.06 Billion at CAGR of 5.70% between 2016 and 2021.
Source: Markets and Markets
What are the applications of Continuous Emission Monitoring (CEM)?
- Monitoring exhaust from power plants and waste-burning facilities.
- Emissions compliance at paper, pulp and other industrial facilities.
- Emissions compliance at cement facilities.
- Emission trading accounting and documentation.
- Air Emissions Reporting Systems (AERS).
Regulatory Authorities: Regulatory authorities prioritize CEMS to enforce emissions regulations, ensure compliance with environmental standards, and protect public health and the environment. They require industrial facilities to install and maintain CEMS to monitor pollutant emissions, report data, and demonstrate compliance with emission limits and regulatory requirements.
Industrial Facilities: Industrial facilities view CEMS as essential for monitoring and managing emissions from their operations. They invest in CEMS to track pollutant concentrations, identify emission sources, and optimize processes to reduce emissions and minimize environmental impact. CEMS data also helps facilities monitor equipment performance, detect abnormalities, and troubleshoot issues to ensure operational efficiency and regulatory compliance.
Analytical Instruments: CEMS utilize advanced analytical instruments such as gas chromatographs, continuous gas analyzers, and optical sensors to measure pollutant concentrations, gas composition, and stack gas parameters with high accuracy and precision.
Data Management Systems: CEMS incorporate data management systems, including data acquisition software, database management systems, and emissions monitoring software, to collect, store, process, and analyze monitoring data. These systems provide real-time visibility into emissions data, generate compliance reports, and facilitate regulatory reporting and data exchange.
Remote Monitoring and Control: CEMS may include remote monitoring and control capabilities, allowing operators to access monitoring data, configure instrument settings, and troubleshoot issues remotely via web-based interfaces, mobile applications, or cloud-based platforms.
Pollutant Monitoring Data: CEMS collect real-time data on pollutant concentrations, emission rates, and stack gas parameters using analytical instruments such as gas analyzers, particulate monitors, and flow meters. This data enables facilities to quantify emissions, monitor compliance with emission limits, and identify emission sources for targeted control measures.
Data Analysis and Reporting: CEMS data is analyzed to calculate emissions rates, assess compliance with regulatory limits, and generate emissions reports for submission to regulatory authorities. Data analysis techniques such as statistical analysis, trend analysis, and emissions modeling help identify emission patterns, outliers, and potential compliance issues for corrective action.
Sensor Installation and Calibration: Deployment begins with the installation of monitoring equipment, including gas analyzers, particulate monitors, and data acquisition systems, at appropriate locations within industrial facilities. Sensors are calibrated and configured to measure pollutant concentrations, flow rates, and other parameters according to regulatory requirements and industry standards.
Data Acquisition and Transmission: Deployment includes the setup of data acquisition systems to collect, process, and transmit monitoring data from sensors to centralized monitoring stations or regulatory databases. Data transmission protocols, communication networks, and data logging systems ensure reliable data transfer and storage for subsequent analysis and reporting.
Case Studies.
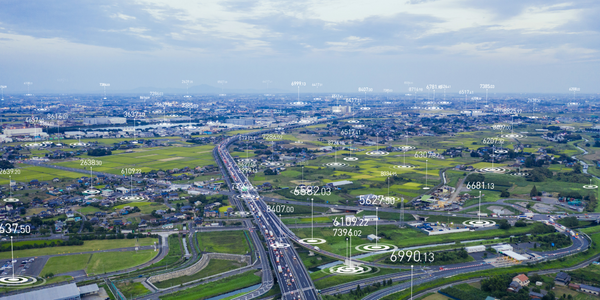
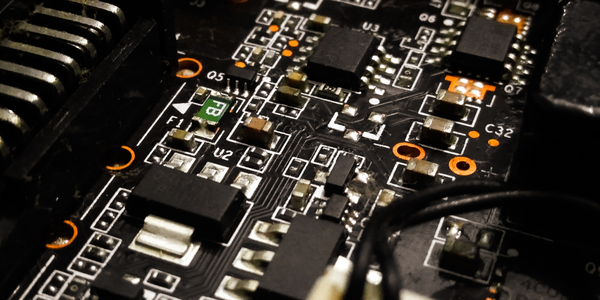
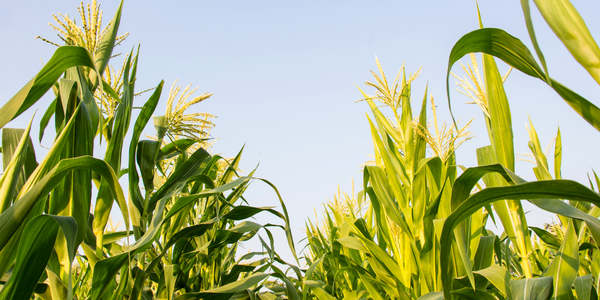