Improving Quality Performance in Packaging with IoT: A Thermo Fisher Case Study
Technology Category
- Drones - Drone Payloads & Accessories
Applicable Industries
- Packaging
- Transportation
Applicable Functions
- Maintenance
- Quality Assurance
Use Cases
- Infrastructure Inspection
- Visual Quality Detection
Services
- Testing & Certification
- Training
About The Customer
Thermo Fisher is a renowned global provider of scientific research services, offering an unmatched combination of innovative technologies, purchasing convenience, and comprehensive support. The company's packaging department in Cincinnati, Ohio, is a critical part of its operations, responsible for ensuring the safe and efficient packaging of their products. However, the department was facing significant challenges in terms of quality issues and lack of standard processes across shifts, which were affecting its overall performance and efficiency.
The Challenge
Thermo Fisher's packaging department in Cincinnati, Ohio, was grappling with significant quality issues, primarily line clearance and inspection failures. These issues were causing inefficiencies and disruptions in their operations. The department was also struggling with the lack of a standard process across all shifts, leading to inconsistencies and misalignments between different groups and supervisors. The goal was to establish a standard process throughout the department, align all four shifts for better cohesion, and train operators to keep the line running smoothly.
The Solution
Thermo Fisher turned to SwipeGuide, an IoT solution, to address these challenges. SwipeGuide was successfully implemented in the packaging department, establishing a standard process to align the shifts and train operators. This solution not only provided a platform for standard operating procedures but also facilitated easy access for operators to understand the correct way to perform tasks. Furthermore, the process flow was adjusted to ensure proper execution. The implementation of SwipeGuide also led to quality performance improvement and waste reduction by introducing quality checks at capper machines and bottling machines, thereby reducing downtime.
Operational Impact
Quantitative Benefit
Case Study missing?
Start adding your own!
Register with your work email and create a new case study profile for your business.
Related Case Studies.
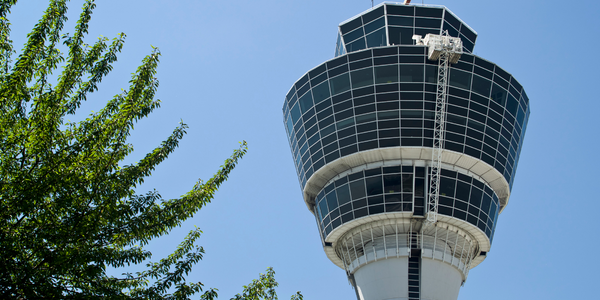
Case Study
Airport SCADA Systems Improve Service Levels
Modern airports are one of the busiest environments on Earth and rely on process automation equipment to ensure service operators achieve their KPIs. Increasingly airport SCADA systems are being used to control all aspects of the operation and associated facilities. This is because unplanned system downtime can cost dearly, both in terms of reduced revenues and the associated loss of customer satisfaction due to inevitable travel inconvenience and disruption.
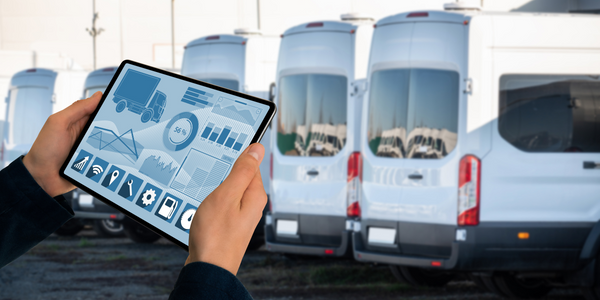
Case Study
IoT-based Fleet Intelligence Innovation
Speed to market is precious for DRVR, a rapidly growing start-up company. With a business model dependent on reliable mobile data, managers were spending their lives trying to negotiate data roaming deals with mobile network operators in different countries. And, even then, service quality was a constant concern.
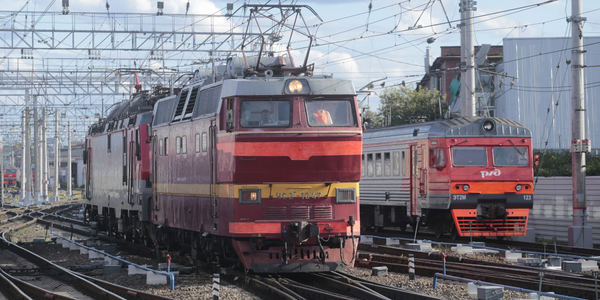
Case Study
Digitize Railway with Deutsche Bahn
To reduce maintenance costs and delay-causing failures for Deutsche Bahn. They need manual measurements by a position measurement system based on custom-made MEMS sensor clusters, which allow autonomous and continuous monitoring with wireless data transmission and long battery. They were looking for data pre-processing solution in the sensor and machine learning algorithms in the cloud so as to detect critical wear.
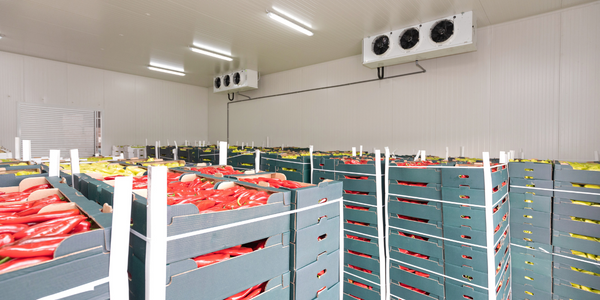
Case Study
Cold Chain Transportation and Refrigerated Fleet Management System
1) Create a digital connected transportation solution to retrofit cold chain trailers with real-time tracking and controls. 2) Prevent multi-million dollar losses due to theft or spoilage. 3) Deliver a digital chain-of-custody solution for door to door load monitoring and security. 4) Provide a trusted multi-fleet solution in a single application with granular data and access controls.
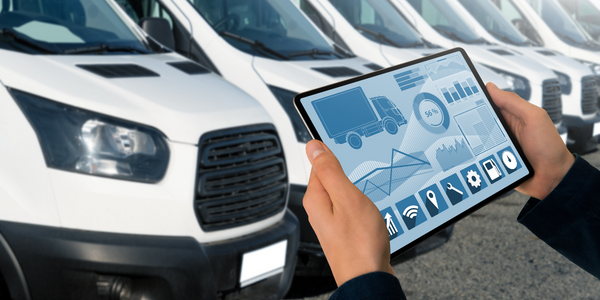
Case Study
Vehicle Fleet Analytics
Organizations frequently implement a maintenance strategy for their fleets of vehicles using a combination of time and usage based maintenance schedules. While effective as a whole, time and usage based schedules do not take into account driving patterns, environmental factors, and sensors currently deployed within the vehicle measuring crank voltage, ignition voltage, and acceleration, all of which have a significant influence on the overall health of the vehicle.In a typical fleet, a large percentage of road calls are related to electrical failure, with battery failure being a common cause. Battery failures result in unmet service agreement levels and costly re-adjustment of scheduled to provide replacement vehicles. To reduce the impact of unplanned maintenance, the transportation logistics company was interested in a trial of C3 Vehicle Fleet Analytics.
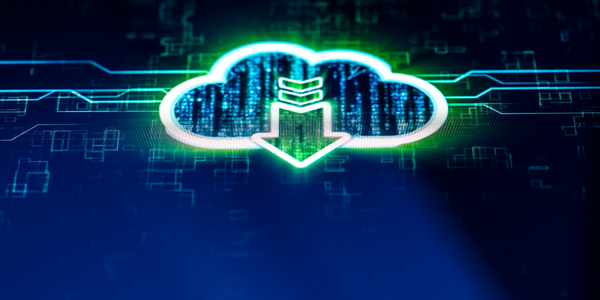
Case Study
3M Gains Real-Time Insight with Cloud Solution
The company has a long track record of innovative technology solutions. For example, 3M helps its customers optimize parking operations by automating fee collection and other processes. To improve support for this rapidly expanding segment, 3M needed to automate its own data collection and reporting. The company had recently purchased the assets of parking, tolling, and automatic license plate reader businesses, and required better insight into these acquisitions. Chad Reed, Global Business Manager for 3M Parking Systems, says, “With thousands of installations across the world, we couldn’t keep track of our software and hardware deployments, which made it difficult to understand our market penetration.” 3M wanted a tracking application that sales staff could use to get real-time information about the type and location of 3M products in parking lots and garages. So that it could be used on-site with potential customers, the solution would have to provide access to data anytime, anywhere, and from an array of mobile devices. Jason Fox, Mobile Application Architect at 3M, upped the ante by volunteering to deliver the new app in one weekend. For Fox and his team, these requirements meant turning to the cloud instead of an on-premises datacenter. “My first thought was to go directly to the cloud because we needed to provide access not only to our salespeople, but to resellers who didn’t have access to our internal network,” says Fox. “The cloud just seemed like a logical choice.”